It has
become increasing apparent in recent years that there is a lot
of misinformation with regard to the fundamental principles
which govern safe rebreather operations. This is partly due to a
lack of precise information from manufacturers and partly due to
misuse and abuse by divers in general.
Fundamentals
In order
to understand what makes a safe rebreather, firstly one must
understand the fundamental properties that govern a rebreather
design. This can be divided into 4 areas.
-
The
resistive work of breathing (WOB) within the rebreather,
otherwise known as resistive effort
-
The
hydrostatic WOB of the unit when submerged
-
The
absorbent duration
-
The
oxygen control dynamics
Looking
at each in turn.
This is
purely a result of the gas flow restrictions within the unit. In
other words how much the size of the pipes and orifices generate
a resistance to breathing. Such things as small mouthpiece
mushroom valves, small hoses, counter lungs with insufficient
volume or room to expand and long absorbent paths within a
canister are common elements which go to make up a resistive
breathing circuit.
Resistive
WOB is also a function of gas density and hence depth. The
deeper the dive and the higher the gas density, the greater the
WOB. WOB is also a function of ventilation or breathing rate.
The more gas flow (higher breathing rate) the more resistance is
generated. A rebreather that breaths ‘OK’ on the surface may
well not at 40m on an air diluent.
Counterlung position and shape also affect the peak
pressures experienced in a breathing circuit. This is why
current European Standards (EN) and military test standards
insist on a resistive WOB measurement at depth and with
different ventilation rates and in at least two orientations
(swimming positions).
WOB is
also subdivided into two areas of concern. The first is a
short-term effect (breath by breath) and the second, long term
(over a dive). The rebreathers pressure/volume (PV) diagram is
normally like a sideways ellipse, as you breathe out it starts
from the bottom left and moves to the top right. The reverse is
true on inhale. If the ellipse is thin (narrow in the middle)
then the energy (joules/litre) consumed within the breathing
cycle may be small and the long term energy expended also small,
however the higher the angle of the ellipse from the horizontal
and there will be a restrictive feeling at the end each breath.
This can produce very laboured breathing and a poor short term
‘feel’ to the rebreather. This is a function of the unit’s
design in a specific area.
This is
the result of the resistive WOB and the effects of the position
of the counter lungs about the body when the rebreather and
diver are submerged in water. For example, a back mounted
counter lung rebreather may have a good resistive WOB but when
in a horizontal (face down) swimming position the distance,
hence pressure difference between the counter lungs and the lung
centroid, may (when combined with the resistive WOB) create an
excessive pressure which the diver has to suck against in order
to take a breath. In this case the inhale pressure would be
excessive (because the diver is inhaling gas from a lower
pressure) and the exhale would be easy having breathed out into
a lower pressure.
Chest
mounted counter lungs have the reverse affect in the same swim
position.
It would
seem that a perfect solution is an over-shoulder counter lung
upon which any hydrostatic effects have little result. However
if a rebreather has a poor resistive WOB anyway, the combination
of this and any minimal hydrostatic WOB can still mean the unit
has a highly restive breathing circuit and hence has a laboured
breathing ‘feel’. Long over-shoulder counterlungs may also give
poor hydrostatics.
In
summary a rebreathers WOB can only be quantified under a range
of hydrostatic (rotating) positions with additional measurements
at depth. Furthermore, assessing a unit under a range of surface
conditions at undefined ventilation rates is inadequate as it is
only under stressful conditions (and normally at depth) that we
generate high work-rates and this is precisely when the
rebreather needs to have a low WOB.
This is a
greatly misunderstood area. Many manufacturers quote durations
based on simple surface trials which is insufficient and
potential dangerous. Absorbent life is primarily affected by the
following;
-
Amount (Kg or Lbs) of material
-
Type
of absorbent material, it’s granule size and shape (which in
turn affects the WOB) and it’s grade or usage type.
-
Water
temperature
-
The
absorbent canisters ability to insulate against the water
temperature
-
The
amount of CO2 generated by the diver
-
The
gas density/depth
-
The
style and design of canister
The
standard CE test for a canister is done at 40m with oxygen in
nitrogen gas mixtures and at 100m with a helium based gas as
diluents, in 4 degrees centigrade water temperature at a CO2
generation rate of 1.6 l/min and a ventilation rate of 40l/min.
Some navies test canister at around 18m and with as low as
0.5l/min CO2 generation. The CO2
breakthrough figure is referenced to 5mb (ref EN14143).
The range
of depths, gas densities, CO2 rates and water
temperatures used in each case can, dependant on the canister
design, give markedly different durations. What is certain from
the data available is that canister durations measured at the
surface are dangerously inaccurate for predicting overall dive
durations. It can be easily shown that for most axial and even
radial canisters the efficiency of the canister decreases
significantly with depth. One canister measured went from 77%
efficient in 15m to 49% efficient in 40m. The 15m duration was 3
hours while the 40m duration was 1 hour and 50 minutes.
The
‘saving grace’ of currently available designs is that most
people cannot maintain rates of 1.6 l/min CO2 or
seldom dive in 4-degree water. However data suggests that as a
method of specifying canister duration, a single hourly rate
independent of primarily depth and gas density, is insufficient
and a range of diving parameter curves may be better employed to
specify a unit’s duration. In other words in order to assess a
rebreather’s suitability for one type of diving over another, it
would seem appropriate to test a unit at a range of depths with
at least air and trimix/heliox as gases. To provide a safety
margin, water temperature and CO2 generation rate
should remain constant.
This can
be a mechanical or an electronically controlled device. Which
ever is chosen it is important that the control of the oxygen
level is maintained within certain limits. If decompression is
to be conducted using tables or a fixed PO2 dive
computer, the limits must be accurately maintained. Rapid
excursions to and from depth must also not generate excessively
low or high PO2’s. Ideally any such limits reached
should generate an alarm, as it cannot be relied upon that the
diver will notice especially in a multi-tasking situation. Some
rebreather designs, due to high flow rates within the oxygen
circuit, can generate massive PO2 spikes sufficient
to cause convulsions in a short space of time if left unchecked,
this is an undesirable design feature should an addition valve
fail. Within the CE and most Navy tests is a PO2
tracking control test as well as an upper and lower limit test
after rapid depth changes. With units employing a constant
minimum feed of oxygen, which is supplemented by the diver, this
minimum should not generate the upper or lower test limits
specified.
In
addition to and as a result of the above there is the issue of
‘diver abuse’, in particular with canister duration rules. This
mainly occurs because of a lack of understanding and
information. Common myths seem to be;
-
‘If I
use all my canister duration I can just scrape the top off
the absorbent and add a bit and get more time’.
-
‘When
I have used up all the time on the absorbent I can just dry
it out and use it again’.
-
‘As
long as I fill a canister and seal it I can use the
absorbent anytime in the future’.
-
‘If I
partly use a canister I can seal it and use the rest at
anytime and get the same duration’.
-
‘If I
fully use a canister I can leave it 24 hours to recover and
then get more time’.
-
‘I
can use my canister at any depth and get the same duration’.
-
‘I
can use my rebreather with any gas and get the same
duration’.
-
‘I
can use my canister in any water temperature and get the
same duration’.
-
‘If I
run out of absorbent time underwater I will get a small
headache and have time to deal with it’.
All of
these assumptions have problems in varying degrees of severity.
The bottom line is that while the sport of rebreather diving is
increasing, unless the education curve follows it, there will be
more incidents, most of them avoidable and some of them lethal.
Rebreathers are life support equipment and as such should be
tested and manufactured to a standard. In
Europe such a standard exists (EN14143). This
standard details many tests from work of breathing (WOB),
through CO2 canister duration to user interaction and
use.
When
purchasing a rebreather it is wise to ask the manufacturer for
any test data or to which standard it has been tested. A
fundamental test is WOB (see graph below). WOB tests the effort
needed to breath from the rebreather, it is a measure of the
resistive breathing circuit i.e. the sum of all the resistance
to gas flow in the circuit.
The graph
below shows the peak to peak pressure experienced by the lungs
(top of the loop to the bottom), this is the short term ‘feel’
of the circuit. Small peaks and troughs at each end are the
effect of the opening of the mushroom valves. The area inside
the loop is measured in joules/litre and while having a short
term effect, produces the longer term feel of the system. i.e.
Just how exhausted you get after a period of use.
The lines
at +/- 25mb are the limits at which the human body can easily
function for a period.
This test
is conducted at a range of flow rates, depths and gas densities.

Another
important test is the CO2 canister duration. Two critical points
are highlighted 0.5% Kpa and 1% Kpa. This is equivalent to 5mb
and 10mb of CO2 at depth. 0.5% is seen as the time
limit to which the rebreather should be specified. The 1% figure
is seen as the safety limit and can range from as little as 10
minutes past the 0.5% limit to over an hour dependant on
canister design.
As
already mentioned this is massively affected by depth, cold, gas
density and CO2 generation rate.
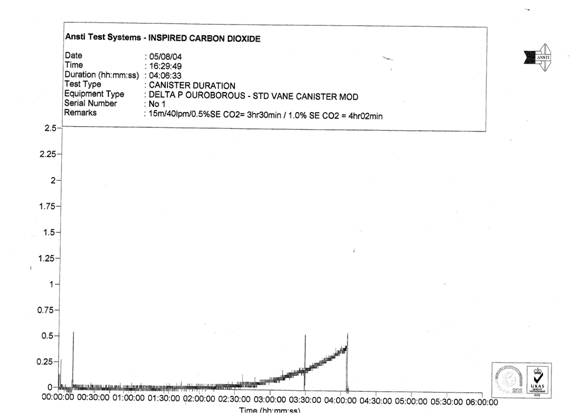
Again
when purchasing a unit is it vital you understand the units
tested duration with all the mentioned variables.
Gaseous
CO2 detection systems are now available (Ref.
Sentinel, Rebreather VR Technology). While thermal monitoring
has some uses, its’ information can be mis-leading under certain
circumstances and is not a finite indication of breakthrough or
time remaining.
Laboratory CO2 detection equipment relies on the fact
that CO2 (and other gases) absorb a part of the infra
red light spectrum. Filament bulbs, detectors and filters are
used to measure the amount of light absorbed and hence the CO2
level. In rebreathers, several problems exist. The first is that
water vapour reacts in a similar spectrum to CO2.
This can give very false readings as the gas cannot be dried
successfully. Also oxygen must be considered, especially if the
bulb breaks! Signal noise, power supplies and a host of other
problems make the implementation of gaseous CO2 systems
difficult for manufacturers. If
you do not have CO2 monitoring then be respectful of
your canister and do not abuse the time limits.
Some
manufacturers realise that packing errors have been an issue
with absorbent and are designing pre-packed cartridge systems
both in granules and ‘solid’ fill options.
In recent
years there has arrived an alternative to granular fill
absorbent materials. Micropore in the USA have produced a material wrap
based system which is basically impregnated with a version of
the granular material but comes as a solid cartridge. This
system offers the following advantages;
-
No
user error in packing
-
Reduced Work of Breathing over granules
The
current trade off is cost and possibly a reduction in life over
granules, but this should change as more and more systems use
it.
It is
very simple to make a rebreather that ‘works’. It is not easy to
make a unit that performs. By that I mean that as the diver
becomes more stressed, the unit needs to have a performance
level that aids rather than impedes the divers’ ability to
survive. Just having a unit that ‘feels’ OK on a dive may not
mean it performs well under stressful conditions. Poorly
designed breathing loops, untried canister designs and
environmentally untested sub-standard components are a recipe
for disaster.
In
summary, there are many elements to rebreather testing (not just
WOB or canister duration) that are critical to defining whether
a unit is suitable for the style of diving and the environmental
challenges a user may but it through.
Read and understand this prior to using any
unit. If you do not understand any or all of this section
please contact your training agency or supplier as appropriate.
Rules for LSS Diving
-
Always do all pre-dive checks.
-
Always pre-breathe the canister for
at least five minutes with your nose blocked!
-
Do not modify the LSS without the
manufacturer’s written consent.
-
Do not use a full-face mask, which is not
designed for a LSS. There is too much CO2 dead-space.
-
Always know your PO2.
-
Never dive a unit you suspect is leaking.
-
Be especially diligent close to and on
the surface where the PO2 is potentially lowest.
-
Never leave your mouthpiece open on the
surface.
-
Never use a pure gas in the diluent
cylinder. You should have a breathable diluent available for
the each section of the dive.
-
Take time to adjust your weight
correctly, do not dive over-weighted.
-
Have two sources of buoyancy and buoyancy
inflation.
-
Practice a skill on every dive.
-
Avoid unnecessary mask clearing.
-
Regularly disinfect the unit.
-
Never dive a re-packed canister.
-
Never hold your breath during an ascent
-
Do not dive with a low battery alarm.
-
Change all main electronic batteries at
the same time.
-
Always carry bailout gases of sufficient
volume for the planned dive as per your training agency
recommendations.
|