Jan Jahns is a diver but above all a physicist, having a lot of
experience with CMF systems. I have asked him if he had the time to write an
explanatory article regarding ‘gassflow through an orifice’. I am therefore
delighted that I have now been enable to publish this article. Do not be
mislead by long equations, eventually they are simplified and can be applied
more easily. By supplying me with this article, Jan Jahns has built a bridge
between science and practice. I therefore would like to thank him for this
enormous effort. In the text I added some hyperlinks and some photo’s to
further illustrate the text. Jan: thank you very much for this fantastic
job!
|
Mass flow
through an orifice
Author: Jan Jahns
Edited: Janwillem Bech |
 |
 |
|
Introduction:
When designing
rebreather the problem of estimation of the mass of
gas
flowing through the orifice (nozzle) of the dosing facilities arises. As
such unit a pressure reduction valve mostly serves followed by the nozzle
through which the gas flows into space where the ambient pressure reigns.
Often double nozzles are used to prevent problems with clogging of one of
them. The gas flows obviously from the place of higher pressure p0
to place of a lower one (p1) and during this
process expands. This process cannot be described by the commonly used
equation of state p.v = R.T, which in principle describe a slow
sequention of equilibrium states. Now the process is fast,
adiabatic, without sharing heat with the
surroundings. In the
Ideal Gas approximation
(it´s also our case) it could be described by the socalled
adiabatic equation
p.vk
=const
Here
k
is also called
Poisson constant given by expression
k
=cp / cv
which states
that
k
is
the ratio of specific heats c measured at constant pressure and
constant volume.
The values of
k
are specific for each gas and from thermodynamics can be by simple reasoning
derived that approximately :
1,67 for monoatomic molecules (e.g. He, Ar)
k
= 1,40 for biatomic ones ( e.g.O2, N2, air,
nitrox)
1,33 for tri+atomic (e.g.CO2 ...)
Experimentally
estimated data for gases in our interest can be found in the included table
together with their densities (specific masses)
rn
at normal conditions (temperature 0°C, pressure 1bar =105 Pa)
and with their molar masses Mm.
For mixes of
gases the relevant values can be obtained by means of the
weighted mean values. E.g. the value of
k
of Nitrox 32/68 can be calculated as
k
= 0,32
×
kO2
+
0,68 ×
kN2
= 0,32
×
1,416 + 0,68
×
1,404 =
1,408.
|
INTERMEZZO WEIGHTED
MEAN VALUE (thanks J.W. Rotteveel)
In this example:
0,32 x kO2
+ 0,68 x kN2
0,32 x 1,416 + 0,68 x 1,404
k
=------------------------------------------------
= --------------------------------------------------- = 1,408
0,32 + 0,68
1
|
Gas |
k |
rn(kg/m3) |
Mm(kg/kmol) |
air |
1,406 |
1,276 |
28,96 |
N2 |
1,404 |
1,234 |
28,01 |
O2 |
1,416* |
1,409 |
32,00 |
He |
1,630 |
0,176 |
4,00 |
Ar |
1,668 |
1,759 |
39,95 |
Ne |
1,64 |
2,277 |
50,49 |
CO2 |
1,304 |
1,951 |
44,01 |
H2 |
1,41 |
0,0089 |
|
|
*
published values of
k
lie in the range 1,40 -1,416 |
The
equation of adiabatic change of state can be also expressed in other
form:
r0/r
= (p0/p)1/k
=(T0/T)1/(k-1),
in which
r
is
density and T is the thermodynamic temperature (in kelvins).
|
 |
Flow velocity:
Consider
ideal gas flowing out from a vessel in which its pressure, density and
(thermodynamic) temperature are denoted as p0 ,r0
and T0 into the environment of pressure p through
an orifice of diameter d as depicted above.
As usually the
energy conservation law must be fulfilled expressed in the case of flowing
media by the
Bernoulli equation. This equation states that in each moment the sum
of kinetic and potential energies is constant:
p
w2/2 +
òp0
(dp/r)
+g×h
=const.
In this
equation the first term represents the kinetic energy (w represent
velocity), the second and third ones represent the potential energy. In form
of integral (second term) the pressure energy is expressed, which is of the
main importance for gas in contrary to the third term representing the
gravitational energy which concerns much more liquids and can be neglected
in the case of gas calculations.
Let us suppose that gas starts flowing from a still state ( which is not
exactly true as our reasoning concerns the intermediate pressure space into
which the gas flows from the high pressure and moreover a little bit cooled
by the expansion. The error introduced by the neglecting of those facts is
allowable). Then the constant on the right side of the equation can be put
equal zero and we can get
p
w2/2 = -
òp0
(dp/r)
Involving the
expression for
r
from the adiabatic equation and solving the integral we obtain for the gas
velocity expression
w2
= ... = [2.k/(k
-1)].p0/r0
. [1 -(p/p0) (k
-1)/k]
One remark:
this expression is usable to calculate flow at „subsonic“ velocity as
shall be explained later.
The gas velocity in the narrowest („critical“) place of the nozzle cannot be
higher than the local sound velocity. But the sound velocity is given by
c =Ö
(dp/dr)
Involving
again the
r
from the adiabatic equation and differentiating we obtain at the end
c2
=...=k.p0/r0
.(p/p0) (k
-1)/k
Should the
flow velocity be sonic (equal the velocity of sound) we have to put w2
=c2 and from equations derived we obtain that for the ratio
p/p0 (i.e. for the ratio of the outlet to inlet
pressures) following condition has to be fulfilled:
pcrit
/ p0 =[2/(k
+1]
k/(k
-1)
=B .
Here pcrit
is the critical pressure in the critical section of the nozzle and from
the formula follows that if the outlet pressure p is lower or equal
to pcrit , i.e. if p/p0
£
B
holds in the critical section the local sonic velocity wcrit
is achieved which cannot be exceeded by no increase of the inlet pressure
p0. The local velocity is emphasized as the
temperature differs here from the inlet gas temperature as will be shown
later.
Involving the
ratio into the formula mentioned above we obtain the critical velocity as
wcrit
=Ö[
2×k/(k
+1)×p0/r0
]
=Ö[
2×k/(k
+1)×pn/rn
×T0/Tn
],
as from the
ideal gas state equation applied onto the non expanding gas is
p0/r0
= pn/rn
×T0/Tn
.
(Here the
subscripts 0 and n denote the relevant variables in the inlet
side and in the normal conditions).
inserting
e.g. the value of
k
for biatomic gases gives the value B=0,528.
The values of
the inverted ratio p0 /pcrit =1/B
lie for the breathing gases in the range 1,90 -2,05, i.e. p0
/pcrit in average aproximately equals 2. It
means again that the inlet pressure p0 being
at least the double of p -the outlet one -the velocity in the nozzle
is sonic. But being lower, e.g. p0 =1.5 p
the velocity would be subsonic.
The above
reasoning implies following: holding the inlet pressure p0
constant (independent of depth) and equal 10 bars (absolute) the
velocity (i.e.also the gas flow as we´ll see later) is sonic up to depth in
which the ambient pressure is half of it, i.e. up to 40 meters, in which the
ambient pressure is 5 bars. The velocity in the nozzle of air whose
inlet temperature has been 0°C is in each depth up to 5 bars 303 m/s. But
going deeper the velocity decreases onto 230 m/s in 60 m
according
w =Ö{
[2.k/(k
-1)].p0/r0
.[1 -(p/p0) (k
-1)/k]}
), onto
105 m/s in 80 m and the flow would stop in 90 m (where ph
=10 bar
ºp0).
The density
and temperature of flowing gas in the nozzle is possible to calculate from
the formulae
r
crit =r0
×[pcrit/p]1/k=r0
×
[2/(k
+1)]
k/(k-1)=p0×rn
/pn
×T0/Tn
×
[2/(k
+1)]
k/(k-1)
Tcrit
= 2×T0
/(k
+1)
Their values
in the example given above are
r
crit =6,73 kg/m3 , Tcrit = 227 K (t =
- 46°C).
|
Amount of gas flowing through orifice:
The mass
flowing through the orifice in a time unit dM/dt can be calculated as
dM/dt = S×
r×
w,
where S
denotes the area section of the narrowest part of the nozzle (S =p
×
d2 /4
in the case of
circular orifice, d being the orifice diameter) and
r,
w
are already known density and velocity in the orifice.
The
amount of gas flowing through the orifice is more frequently expressed in
term of „normal volume“ units in prescribed time (e.g.normal liters in
minute, l/min or lpm). As „normal“ the volume at normal atmospheric presure
is ment (i.e. „at the sea level“). This variable, denoted Dn
here, can simply be estimated from the mass flow dividing it by the normal
density
rn
of the gas (Vn =M/rn
),
i.e.:
Dn
=dVn /dt = 1/rn×
dM/dt = 1/rn×
S×
r×
w.
For the
sonic flow the critical values
rkrit
a
wkrit should be inserted giving
Dn
=S
×p0
×Ö{k×[2/(k
+1)](k+1)/(k-1)×
1/(bn×rn)}×Ö
[Tn/T0]
In this
formula some constants specific for specified gas take place which can be
assembled into one constant giving a simple expression:
Dn=
d 2×p0
×A1×Ö
[Tn/T0],
in which
A1
=p/4×Ö{k×[2/(k
+1)](k+1)/(k-1)×
1/(bn×rn)}
=const
.
Including into
the constant also conversion factors for units to be used (pressure in bar,
nozzle diameter in mm and flow in liter pro minute) and neglecting the
temperatur
ratio then
constant A can replace the A1 giving the
possibility to calculate the flow of commonly used brething gases in a very
simple manner:
Dn=
d 2×p0
×A1
By a simple
analysis the following formulae can be found for this constant:
A = 8,65 for pure O2
A =9,233 - 0,00588×O2
[%] for nitrox
A =9,71 +0,0011×He[%]2
for trimix (best fit for He in the range 10 -50 %)
Example:
TMX20/50, d =0,31 mm, p0 = 11 bar :
Dn
=A×p0×d2
=13,17 l/min
(more
precise calculation gives 12,91 l/min)
It should be
emphasized that the constant was derived for circular smooth orifice what is
the shape ensuring the best flow as the ratio of the wall surface to the
inner volume is the lowest from all possible orifice shapes. The walls and
their quality affect (i.e. slow) the flow of the gas by friction and
turbulence. So using an orifice of another shape the flow would be lower,
the lowering being expressed by a certain constant known as shape factor.
|
Rebreather calculations:
In
calculations made above were as p0 and pamb
the intermediate and ambient pressures (in bar) denoted. Here
p0
is
constant when the pressure reduction valve is not compensated to ambient pressure,
and
increases with increasing depth by h[m]/10 when
compensated (as in common regulator).
|
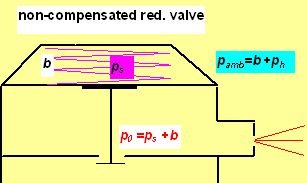 |
In this
picture b represent the normal atmospheric pressure (1 bar usually),
ps the pressure exerted by the spring force (in fact the
gauge IP) and ph the hydrostatic pressure. pamb
is for the ambient pressure (absolute).
The
non-compensated pressure reduction valve (PRV) is designed for constant
mass flow applications, i.e.:
So the maximum
allowed depth is this one, in which the sonic flow is
maintained, i.e. in which the ambient pressure pamb is
roughly equal the half of intermediate pressure p0. In
deeper depths the flow becomes subsonic and the mass flow
decreases as the depth increases.
Example1:
if p0 =11 bar then the maximum allowed depth (in which the
flow becomes subsonic) lies in about 45 meters (pamb =5.5
bar).
Example2: with p0 =11 bar and orifice diameter d
=0,08 mm the flow of pure oxygen is 0,61 lpm in each depth up to
about 45 m, but in depth of 90 m the subsonic flow gains only 0,36 lpm ! To
be usable to 90 m you need p0
³
20
bar. But then the orifice must be smaller to restrict the flow which would
reach 1,1 lpm using the original one. You have to choose 0,06 mm to gain
0,62 lpm or 0,07 mm to gain 0,85
|
 |
 |
In
compensated pressure reduction valve (the same as the 1st stage
of common regulators) with growing depth increases also the intermediate
pressure. From reasonings given above we know that higher p0
results also in greater flow (remembering Dn =A×p0×d2
?). Denoting p00 the (absolute) intermediate pressure at
surface and p0h the IP in the depth h (h in
meters), then p0h = p00 + h/10
( p in bars).
The gas dose
Dh
in
depth is given by the surface dose D0 multiplicated by the
ratio of intermediate pressures in the depth to the surface one,
i.e. by
p0h/ p00
,hence
Dh =D0 · p0h/ p00
= D0 · (p00 +h/10) / p00 = D0
· (ps +b +h/10) / (ps +b)
and the dose
grows linearly with the depth. But in certain depth hcrit
-given by the constant B -the ambient pressure becomes critical
compared to the pressure p0h
and the flow
ceases to be sonic. Although the flow always increase with deeper depth the
increment is no more linear as can be seen in the following plot in which
for the sake of demonstration the ps =IP0 =6 bar was
chosen and flow through two nozzles each of diameter 0.2 mm was calculated :
|
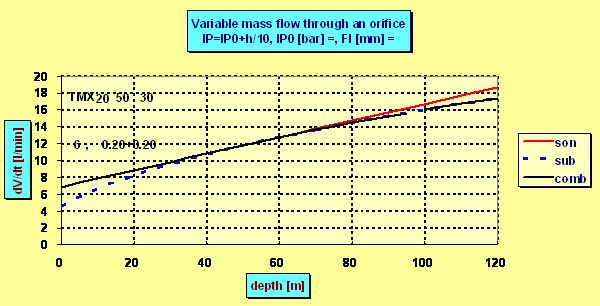 |
The mentioned
critical depth can be easily found as in this depth the intermediate
pressure p0h must be roughly 2 times greater then the
ambient pressure pamb , i.e. ps + pamb
=2×
pamb
. That means
that the flow ceased to be sonic in the depth in which the ambient pressure
pamb equals the „spring pressure“ ps
which in fact is the (over-)pressure measured by an IP gauge. E.g. having
ps =10 bar, the flow becomes subsonic in 90 m, where
pamb = 10 bar. But even in 200 m the actual dose is only
5% lower than the flow predicted by the linear equation as although the
velocity drops onto only half of the sonic velocity the pressure increment
increases the density
r0
and so also the flow.
What are the advantages and disadvantages of both arrangements ?
The advantage
of the non-compensated PRV is maintaining the constant mass flow in
the range of proper depths. So also the estimated dose D of the
supply mix is constant and according the well known equilibrium equation of
SCC
fiO2
=( fsO2
×
D -SO2 )/( D -SO2
), *)
(here fsO2
being the fraction of O2 in the supply mix and SO2
the oxygen consumption rate of the diver) also the calculated
fraction of oxygen in counterlung fiO2 remains constant.
Choosing the IP reasonably high and of course choosing also the proper
nozzle the flow ensures fiO2 staying in proper, i.e.
safe margins. Also the fractions of other constituents of the inhaled mix (N2,
He) can be calculated and used for decompression purposes. Having the p0
chosen as 18 bar, the constant flow of the mix is ensured up to about 80
meters. (But diving deeper then about 40 m trimix or heliox should be
employed). The same dose in any depth enables also precise prediction of the
supply gas consumption
Regarding the
KISS and its clones -the constant submetabolic dose of oxygen must be
unevitably kept in each intended diving depth and so the non-compensated PRV
has to be used in the dosing system. As the dose required is small (less
then 1 lpm) the orifice area section should be also small as explained in
the example 2 above. So to prevent the clogging of such tiny orifice a
10-20 microns filter has to be inserted into the flow path before entering
the orifice. Using metering valve instead of circular orifice can improve
the situation as eventual clogging would occur only in a part of the
flow-through section. But I´m not sure how outer temperature differences
affect the flow in the valve.
Employing the
compensated PRV in the SCR results in doses Dh
depending on the depths. As disadvantage only the not-so-precisely
predictable and higher gas consumption could be considered. On the other
hand the enhanced flow „improves“ the oxygen fraction fiO2 in
the inspired mix, i.e. the fiO2 draws nearer and faster
to the supply fraction fsO2 compared to the steady flow.
So the estimation of fiO2 can always be made by the help
of the above equilibrium equation using the surface dose D0
and taking into account the fact that the calculated value of fiO2
is only a little bit underestimated. Moreover the flow is maintained to be
sonic much deeper as shown above and even subsonic flow ensures doses large
enough. So the use of much deeper depth of the system is enabled. To
estimate the gas consumption during the dive simply the consumption in the
greatest depth should be done according the formula
Dh =D0 · p0h/ p00
= D0 · (p00 +h/10) / p00 = D0
· (ps +b +h/10) / (ps +b)
given also
above. Remember only, that ps is the IP measured,
b =1 (bar) and
D0
is
the surface dose.
Estimation of
the flow is the last topic discussed here.
*)
BTW the fiO2
is higher then calculated here using separated exhale bellow (as is common)
giving also piO2 higher by about 5 kPa (0,05 bar) in any
depth.
|
Measuring the gas flow of mixes.
To estimate
the flow of gases mostly the float (e.g. ball) flow meter is used.
|
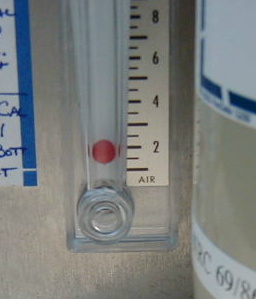 |
The flowmeters
are calibrated for certain gases or their exactly definited mixes -oxygen,
air, nitrox 32/68 etc. In the need to employ the flowmeter for another mix,
e.g. for trimix, the following considerations could be made:
The force F1
holding the float in certain position (marked as a certain flow) in the
gravitational field is proportional to the kinetic energy of the flowing gas
F1
=C×
E1 =C×1/2
×
r1
×
v12,
in which
formula the subscripts „1“ concern the original gas flowmeter is designed
for and C is the constant proportionality factor (incl. shape factor of the
float). The mark on the pipe concerns the flow velocity v1
of the specified gas. If another gas flows through the flowmeter then
its energy is
E2
=1/2
×
r2
×
v22
and on the
same mark also the energies of both gases should be the same:
E2
= E1
Inserting here
the above mentioned formulae the following expression can be obtained:
v2
/ v1 =Ö
(r1
/r2
) .
i.e. the ratio
of the gas velocities is inversely proportional to square root of their
densities. Densities are proportional to molar masses Mm
of the gases which could be easier found then densities themselves and as
the flow D is proportional to the velocity the expression for flows
of the gases can be written as
D2
= D1×Ö
(Mm1 / Mm2 )
As said in the
introduction part for mixes of gases the relevant values can be obtained by
means of the weighted mean values. E.g. the value of Mm1
of air (21 % O2, 79 % N2) can be calculated (using
table in the introduction part) as
Mm1
=(0.21×32
+ 0.79×28)
=28.84 (kg/kmol).
Wishing to use
air flowmeter to measure flow of trimix TMX 20/50 (20 % O2 , 50
% He and 30 % N2), then
Mm2
=(0.2×
32 +0.5×
4 +0.3×
28) =16.8 (kg/kmol).
Inserting
obtained values into the square root :
Ö
(Mm1 / Mm2 )
=Ö
(28.8 / 16.8) =1.31 and e.g. with the float on the 10 l/min label (D1=10
l/min) the actual flow of trimix is D2 =13.1 l/min.
Using oxygen flowmeter the label 10 l/min denotes 10×Ö
(32.0 / 16.8) =13.8 l/min.
|
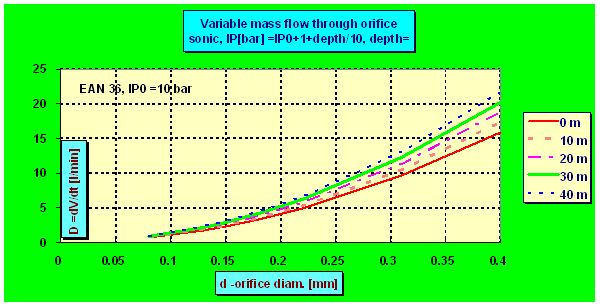 |
One picture
more showing the volume of flowing gas depending on the orifice
diameter and depth as the compensated PRV was used
|
Units
P=
pressure
V=
volume
R=
gasconstant [8,314 J mol-1 K-1]
T=
temperature in Kelvin
Kelvin
= Celsius + 273.15 // Fahrenheit =( Celsius/(5/9)) + 32
k
=cp / cv=
poisson constant
Mm
= molar mass
p0
= pressure before orifice
r0
= density
before orifice
T0
= temperature in Kelvin before orifice
Tn
= normal temperature in Kelvin
Tcrit
= critical temperature in Kelvin
W
= velocity
Wcrit
=critical velocity
g
= acceleration at surface due
to Earth's gravity= 9.8 m/s2
h =
height above ground
c =
characteristic speed
pcrit
=
critical pressure
pamb
=
ambient pressure
r
= density
rkrit
=
critical density
rn
= normal
density
B
=
ratio of the
outlet to inlet pressures
S
=
area section
of the narrowest part of the nozzle (S=p
×
d2
/4)
d
= orifice diameter
A
= constant
B
= constant
PRV = pressure
reduction valve
CMF = constant
mass flow
MCCCR = manual
controlled closed circuit rebreather
IP
= intermediate
pressure
p00 = absolute intermediate pressure at the surface (=ps+b)
p0h = intermediate pressure at certain depth (=ps+pamb)
D = gas dose in normal (surface) liters per
minute
Dh = gas dosis produced
by IP at certain depth h
D0 = gas dosis measured at the surface (open PRV)
Dn
= gasflow through orifice
|
Security check: |
 |
Jan , thank you for your fantastic help
by writing this article for my web! |
If you have information about the theory of the
adjustable needle valve I would be pleased to receive that. I am
looking for information that describes the way the needle valve
is designed and how the form of the needle is related to the
flow. |
|